Finding rare earth elements by hyperspectral imaging
Imagine a world without smart phones, the latest medical imaging or great bass response from your earphones? Nope, nor can I. Worryingly, the continued availability of these essential 21st century pieces of tech is far from certain because they each rely on so-called Rare Earth Elements (REEs). REEs are not particularly rare but they are […]
Raman sets new levels for FFP3 mask efficiency
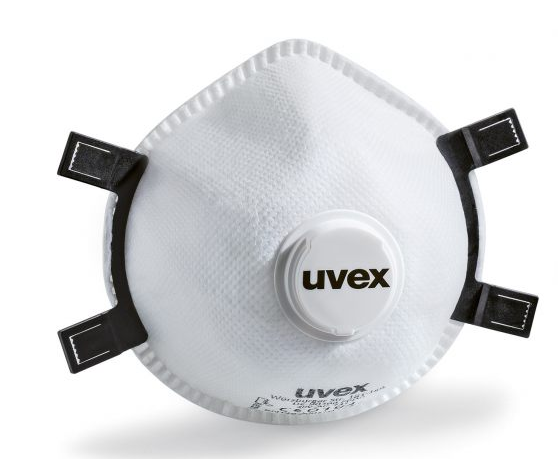
Over the past three months we have all come to know more than we ever wanted to know about face masks. There was a time when most of us encountered face masks only as themes for movies (think Antonio Banderas in Zorro and Jim Carrey in The Mask) or as gloopy brown stuff applied to […]
Gorilla glass under the (Raman) microscope
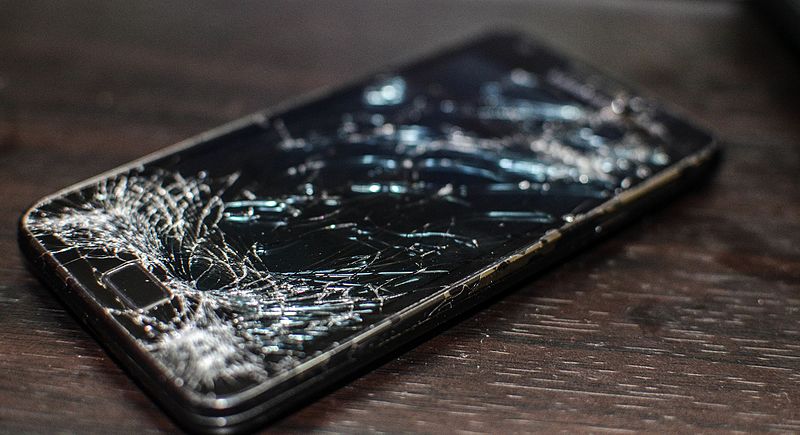
It’s happened to at least one of our smartphones or tablets. Our pride and joy piece of tech gets dented with an ugly crack or scratch. Smartphones are so essential to modern life that we stuff them into bulging pockets and handbags, not noticing what else we also can’t live without. Bunches of keys and […]